Flying Carpet - A tale of magic and Motors.
How do you make a magic carpet fly for Disney’s live action remake of Aladdin?
You get ILM to create you a computer graphics one of course, which they did; but wait a minute. Jasmine and Aladdin have to ride it whilst singing “A Whole New World” and it absolutely has to be the lead actors up close and personal.
The solution was to build a giant robotic carpet, three months of planning, a month of shooting and use a lot of clever mathematics.
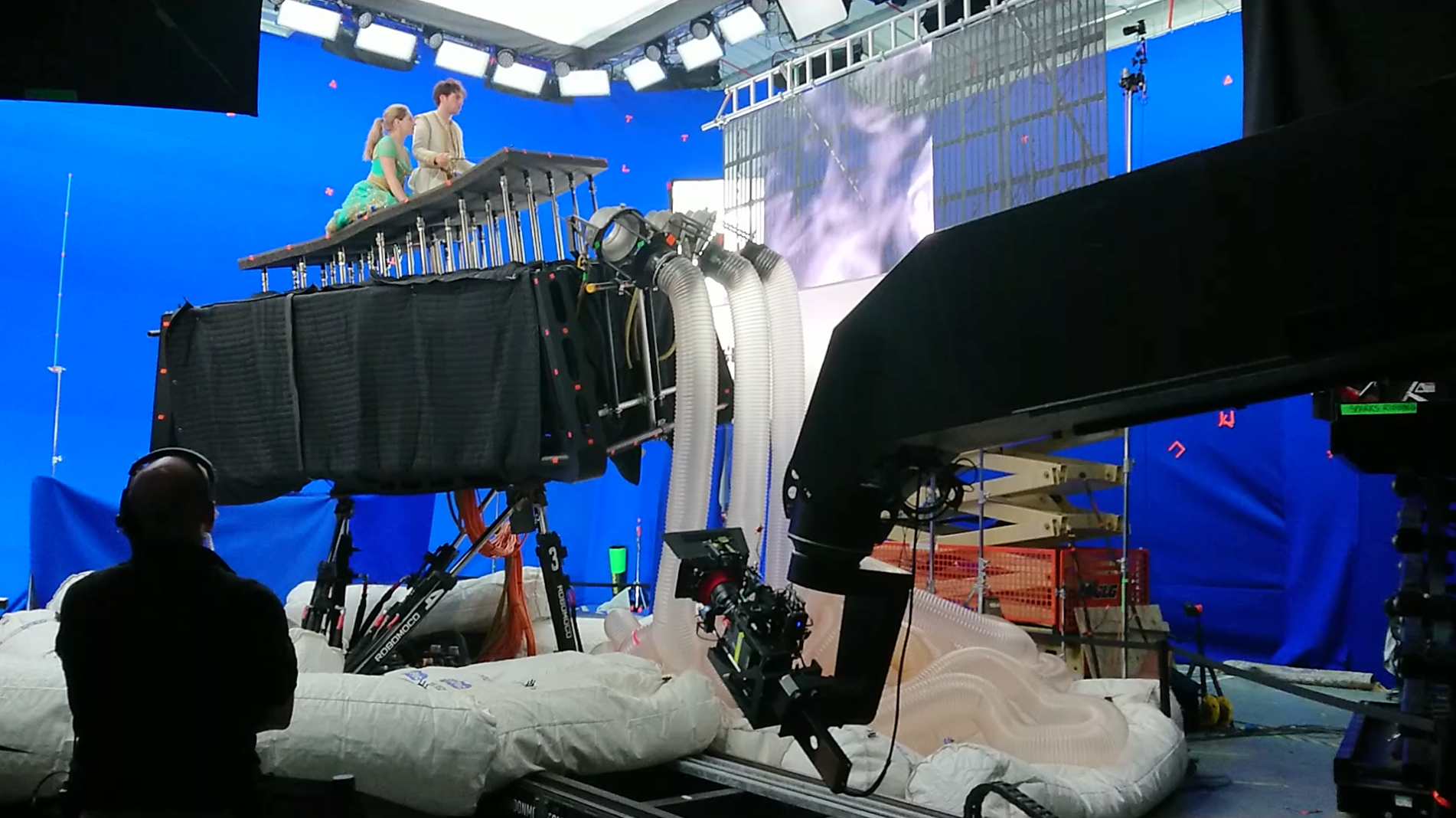
The Statistics
- 3 Sequences
- 73 Shots
- 1,095 motion control data files
- 1,358 number of times shots were run from beginning to end on the machines
- 12 weeks testing
- 4 weeks shooting (brought in ahead of schedule)
- 15 motion control shots filmed per day
- No overtime required
Take4D and Richard Widgery
Virtual Production Supervisor Richard Widgery (from Take4D) was asked to assist in setting up what came to be nicknamed the “Carpet Unit”.
Richard has been creating some of the most extraordinary camera sequences for the past three decades. Known for his work on projects such as Assassin’s Creed, Avengers, James Bond and The Harry Potter Theme Park, Richard’s approach and proprietary technology enables shots that would otherwise be a computer fantasy translate into a practical reality.
Richard is the originator and developer of of CineBridge, a unique tool-set that bridges the gaps between Pre-Production, On-Set Shooting, and Post-Production. It works alongside Pre-Visualisation to plan and simulate real world robotics in advance of practical photography. It generates the actual motion control data to be used on the robots, as well as real time camera tracking and rendering of live images composited against CGI animations. With clear technical plans and layouts, errors are reduced and huge efficiencies achieved throughout production.
The Sequences
There were three main sequences to be tackled; “Carpet Chase”, “Cave of Wonders”, and “A Whole New World”. Two of these were high speed action sequences needing very fast changes of direction and highly dynamic camera work. The other required very large sweeping but subtle camera movement and swaying “boat ride” carpet motion.
The Hardware
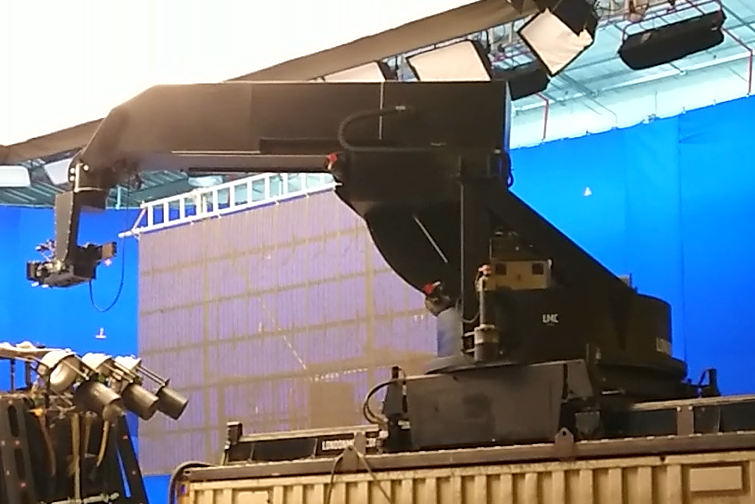
In addition to the computer controlled lighting rig, LED video walls, audio playback and wind machines, there were two main robots used for filming the flying sequences.
The camera, whilst sometimes on a Technocrane, was mainly mounted onto a Cyclops motion control rig provided by London Motion Control.
Richard and LMC have partnered together for many years going back to the days of Harry Potter and the real world limits for that rig were already inside Take4D’s simulator.
The carpet however was custom build. Designed and made by Mark Holt SFX and RoboMoco.
The actors sat on a neoprene mat that had thirty six motorised pins controlling its shape.
The pins sat on top of a seven axis flight simulator, the kind used to train aircraft pilots.
With a combined weight of around 1.5 tonnes, it was all bolted down to the concrete floor and not moved during the entire production.
The data for both systems was provided by Take4D with the carpet pin ripples coming from Proof that were doing the Pre-Visualisation for the film.
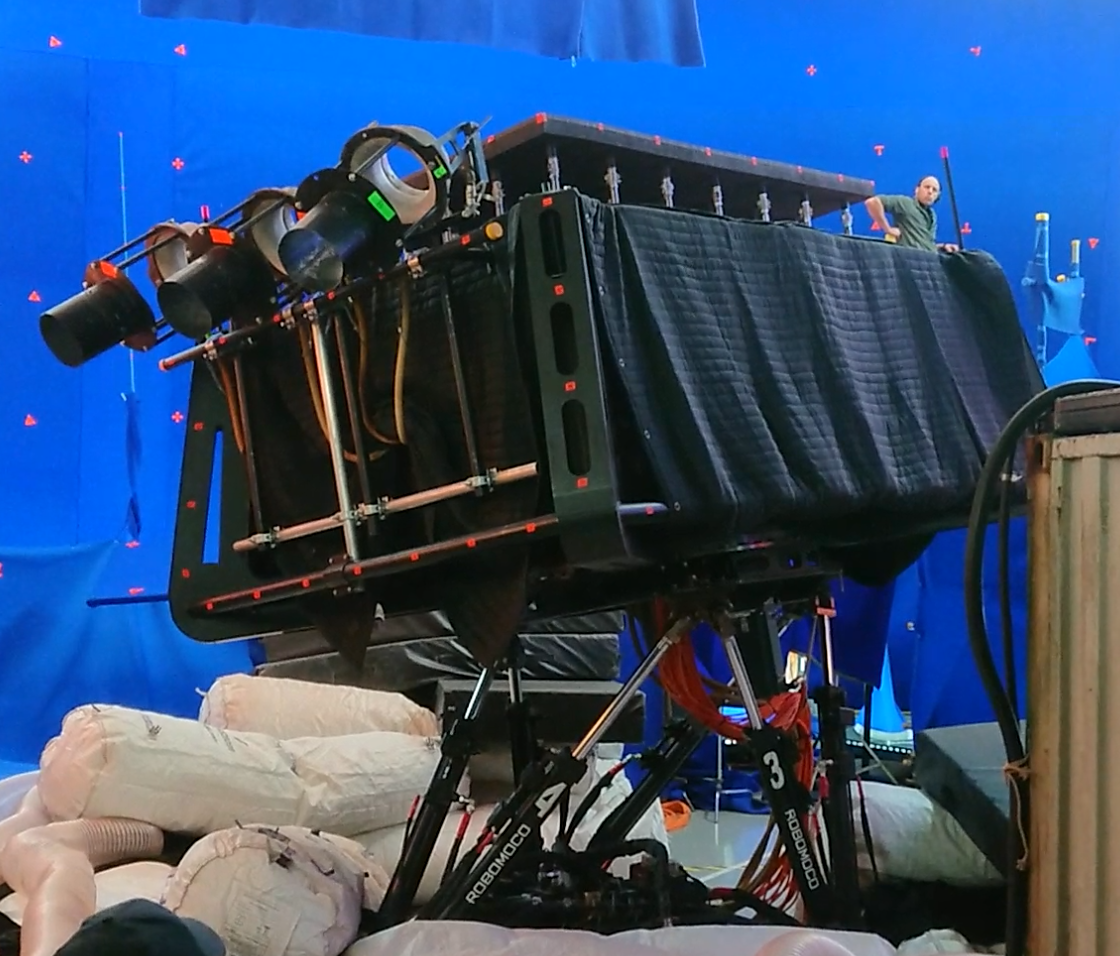
Test Pilot
Being a unique piece of engineering, the carpet had never been operated before. A week was dedicated to testing during which Richard learnt how to fly it.
“We needed to know what it was capable of. How fast can it turn? How far can it bank? What type of motion would make it un-rideable? What would look wrong on camera? We were pushing the rig to its limit, always with one eye on the fact that we could not afford break it. It was a one off build and we had tight time constraints.” Richard said.
“By matching the simulator to the real rig, we could develop shots in software with a very high degree of certainty that they will run on the real machine first time every time.
“We knew that the Pre-Vis animations were going to be too fast and erratic for the real rigs and we needed to find out how much we could get done for real and how much would be added later in post. For example, when doing a sharp banking turn, there was a split between three things; what the flight simulator did; what the pins driving the neoprene mat did, and what would be added by VFX. The flight simulator base, being the heaviest part, could not move as fast as the pins so we split movements into different components depending on their size and speed.”
Safety First – Safety Last
Three months were allocated for the development of these sequences due to the level of testing and safety involved.
“We never ran a new piece of data at full speed first time on any machine. For each machine, we ran the entire move at slower speed first, gradually increased it until we reached 100%. Once the rigs were independently at full speed, we then did the same for all rigs together.”
Every shot was under the scrutiny of stunt supervisor Roy Taylor. He carefully watched the rehearsals and then decided if it was safe to ride by the stunt doubles. Casey Michaels and Luke Gomes were doubling for Naomi and Mena. Once harnessed in place, the procedure was repeated to bring the rigs up to full speed again. At any time as the speed increased they could give feedback or request adjustments to ensure the safety of the lead actors and the ability to deliver a performance whilst riding the carpet.
“Casey and Luke were fantastic. Day in, day out they would ride this rig again and again for shots that sometimes only lasted for a second or two. I think most of the crew were actually a little bit jealous. On a number of the bigger and more dramatic shots, when the camera cut, they had big grins on their faces as if having fun riding a new roller coaster.”
“It ranged between 8-17 times that a new data was run from beginning to end at different speeds before being signed off as ready for the lead actors to ride. At that point the shot was ‘bagged’. If any version changes were to be made to a shot, we started the process over from scratch.”
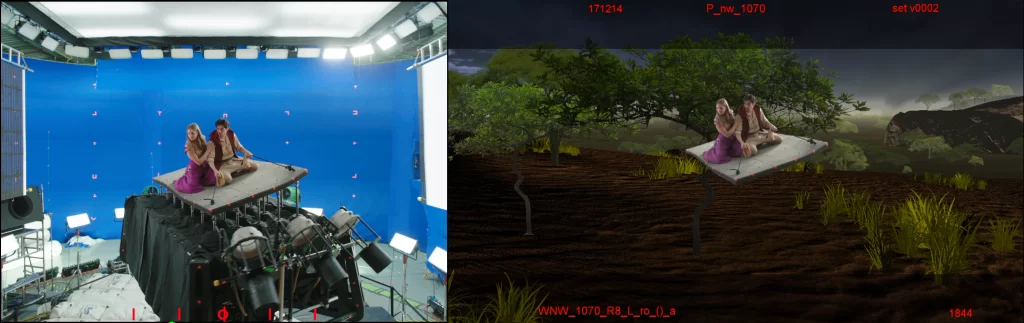
Once everyone was happy with it, the shot was filmed, composited on-set against the original Pre-Vis and sent back into the VFX edit for review.
All the shots needed to be tested and “bagged” before the Christmas break as Main Unit began shooting on January 4th 2018. The process was the same during the shoot. Naomi and Mena were harnessed in and the shots were run up at increases speeds as before so that they could get use to the movement of the carpet.
“Their performances needed to flow with the motion of the carpet and not react against it. Increasing the speed slowly ensured that there were no surprises for them and gave them the opportunity to learn each move before the cameras rolled.”
The Pipleine – Shot-Anim Department
Proof were already working on the Pre-Visualisation of the sequences before the “carpet unit” was set up. Coming from an artistic perspective rather than one of a practical shoot, the Pre-Vis animations were not usable directly on the rigs. The animations were always going to be more dynamic in motion than what the machines could cope with.
Richard established a highly flexible pipeline consisting of a team of expert animators as a dedicated unit he called “Shot-Anim Department”. He used the results of his test flights to assist the team in modifying the Pre-Vis so that they could be applied to the robots via CineBridge.
“Shot-Animation differers from Pre-Vis in that Shot-Anims can be run on the rigs for real, where-as Pre-Vis often can’t.”
Over the three sequences, there were a large number of shots constantly under revision and every shot needed to be modified one way or another.
“It was a learning curve for the team. We really had a great group of animators that quickly learnt what worked and what didn’t. Soon they were able to instantly recognise the changes they needed to make. It became its own kind of language.”
“Version changes were always going to be a challenge with the time we had for mechanical testing. Using CineBridge, we had the ability to replace the original animation with a newer version without changing the work done to make it run on the rigs. Most shot revisions were small re-framing or timing adjustments. By keeping all of the original work, these revisions were extremely quick to re-process massively accelerating the turn around time. I think the fastest revision change was 11 seconds from receiving it to loading onto the machines.”
Up, Down, Up, Down
Adding to the complexity of the logistical planning was the need for the Cyclops camera rig to be raised and lowered on-top of shipping containers many times through-out the testing and main unit shoot. The extra height was needed to get above the carpet and the only way to do it was to raise the entire rig and its track.
Richard, ILM’s VFX Supervisor Dave Seager and 1st Assistant Director Joe Geary co-ordinated on developing daily schedules dependent on the order of the shots coming in from Pre-Vis and where they were in the pipeline.
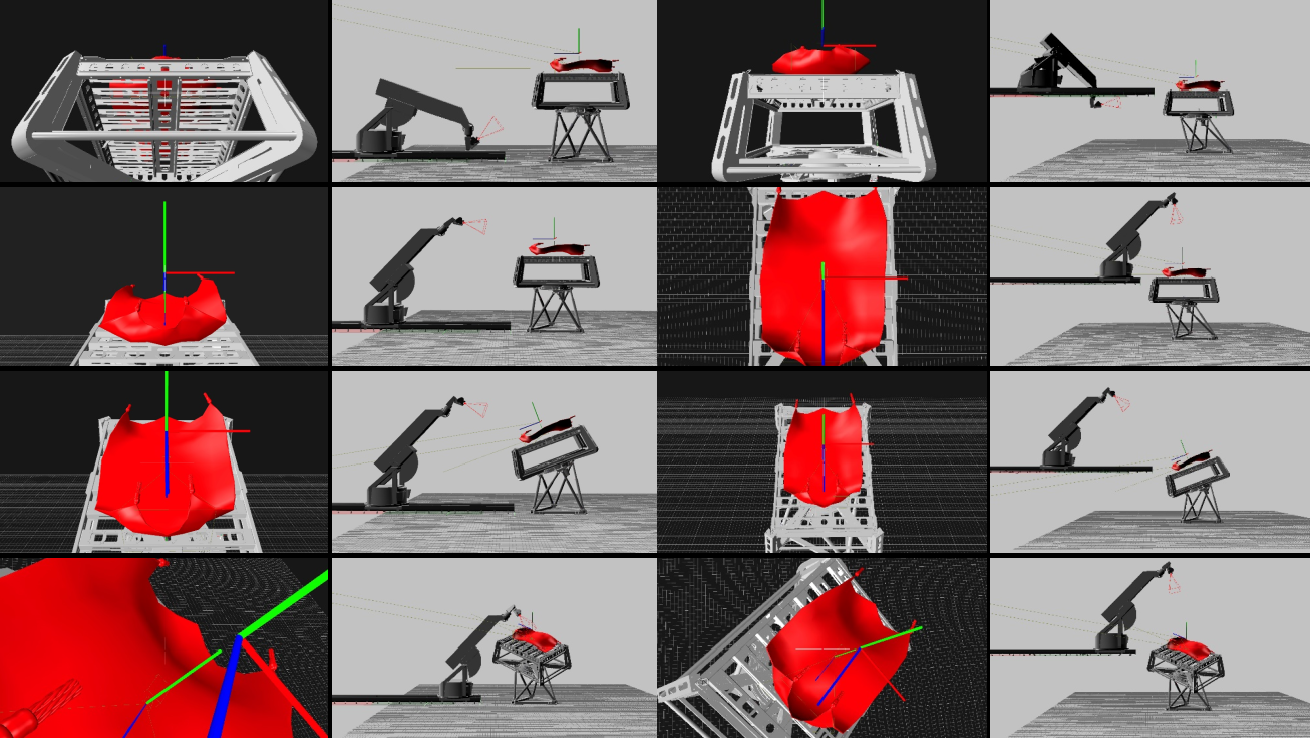
Shooting and Post
Not all shots were derived from the Pre-Vis. Some were “free camera and Waldo” where a Technocrane replaced the Cyclops motion control rig and the flight simulator was hand puppeteered via a glorified joystick called a Waldo. Some shots were even recorded with both techniques to give more creative freedom and choice in the edit.
Where shots were pre-programmed and having them all pre-testing and ready to shoot, meant that up to fifteen motion control shots were filmed a day. Modification were extremely fast due to CineBridge’s non-destructive pipeline.
All the equipment and robots in the studio were triggered by time-code. In the case of “A Whole New World”, this was tied to the audio of the song. Another challenge was that the sequence was under constant editorial revision requiring daily sometimes hourly changes of the performances within the song.
“The creative process on “A Whole New World’ was very fluid. Whilst the geographical location of a flying sequence may not have changed, its position in the song may have, leading to a change in time-codes and lyrics needed to be delivered.”
To assist Post Production and help eliminate the need for reshoots, a complete library of 3D data files was supplied back to VFX containing the workflow from beginning to end of every shot including the changes made to get the moves running on the machines.
The highly efficient “Shot-Amin” Virtual Production Department that Richard created meant that all sequences were filmed a week ahead of schedule on a four week shoot allowing the extra time to be used for pickups and additional creative shots.
Feel free to contact us to discuss your next project of any size and scale.
Find out more about Take4D’s CineBridge and Virtual Production Studio products.